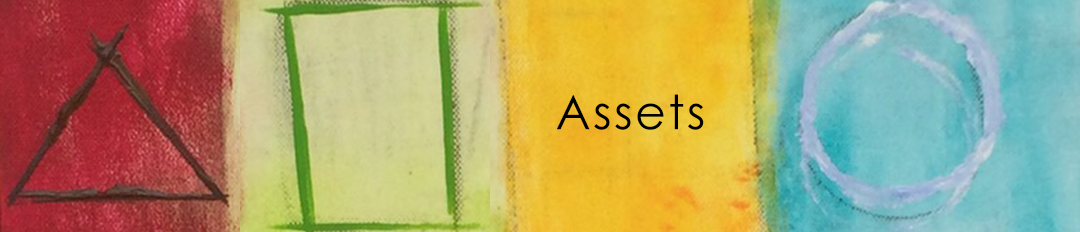
eco-e tech©
eco-e tech stands for the full energy saving and environmental program of eco-e. This includes a thermally enhanced furnace, a two-container scrap preheating and a transformation of the remaining energy after the scrap preheating. With this program energy saving of up to 150 kWh/tliquid steel (ls) and environmental emission as low as 20 kgCO2/tls are feasible. The secret behind this program is a reliable off-gas control, that allows to optimise the transfer of the energy contained in the off gas, the fast-burning pollutants and reactions and the energy needed for cleaning the combustion products in the off gas to the scrap. Importantly, the existing furnace will be fully preserved.
Torus EAF©
The furnace enhancement includes a new off-gas evacuation system which allows to make better use of the energy input, enhances the scrap melting and helps to reduce the electrode consumption. Importantly, the torus off-gas evacuation allows a more equal heat distribution in the furnace eliminating cold spots.
Cool electrode©
The ‘cool electrode’ is a new CCU (carbon-dioxide capture and use) application that allows to reduce the electrode consumption further, supports the foam building of the slag, and induces the stirring of the metal bath by a CO2 injection.
ECOFEEDER©
The ECOFEEDER replaces the existing combustion chamber which exists in all traditional furnaces. There, currently dust settles down, post combustion of CO to CO2 happens and gas speed is reduced. This is exactly what happens in the first container. Additionally, the burn-off of fast-burning pollutants and reactions which are included in the cold scrap support the scrap preheating. The combustion products which are produced are treated in a following burner chamber. The energy needed to treat the toxic and harmful products is then again transferred to the scrap lying in the second container. The ECOFEEDER is designed as an add-on to the furnace. The ECOFEEDER concept includes different designs to best suit your expectations.
More about the ECOFEEDER concept in Downloads (E)
ECOSLAGCAST®
One of the by-products of the steel production is slag consisting of lime (CaO), dolomit (MgO), oxide of iron (FeO) and other elements and compounds. This soup full of impurities and compounds is as hot as the steel. Our target is to separate the useful elements like iron (Fe) from the rest. At the same time we are interested in transforming the bound heat in the slag into electric energy.
The end product, a granulate of 5 to 10 mm slag and separated Fe-containing parts at a temperature below 200°C, directly delivered on a conveyor belt. A dust and water free slag recuperation, ready to be disposed.
ECOSLAGCAST® is a registered trademark of eco-e AG
Efficient slag handling: > 50 kWh/t electrical energy recuperation; metal separation; slag granulation; exit temp. < 200°C
ECOMETVAC®
There are many suppliers of vacuum technology battling for customers. Some of them are even offering vacuum treatment without filters which definitely is wasting money and energy as the dust – yes, there is dust produced – goes to the vacuum production and builds sludge or damages the mechanical pumps, and yes there are issues with filters as the arising metallic magnesium and/or zinc are burning the filter bags, so why not looking at our new edge-breaking new filter solution, which works for VD and VOD as well.
We have some other interesting details in our vacuum offer, e.g. a dynamic slag level detection (no more over flows (working with any vacuum production)).
ECOMETVAC® is a registered trademark of eco-e AG.
IMAGINE
you had a melt shop where no persons would have to work in dangerous positions, where a furnace change would be done in 15 minutes, where everything would be automated from scrap charging to casting, where tap to tap times below 30 minutes could be realized, where furnace teeming and alloying is made together under vacuum, where no fumes and off-gas would escape, where no canopy is needed, where the off-gas temperature is almost stable, where the off-gas energy is reused for scrap preheating and the rest energy for driving a ORC-turbine and where no filter bags are needed, where slag is directly separated from iron and arising free of dust and water ready to further use etc.!
This is what we plan when offering a ‘green field’ melt shop – this is what we call a eco steel plant.